5 Manufacturing Training Challenges An LMS Can Help You Overcome
The need to fill the skills gap quickly is one of the most pressing manufacturing training challenges. But it’s not the only one on the list. Let’s break these challenges down one by one, and see how an LMS can help you solve them and safeguard the future of manufacturing.
1. The Skills Gap Is Huge
The manufacturing workplace is not what it used to be. Automation and computer-controlled machinery are a huge part of the manufacturing process. Very often, they replace manual labor. The need for tech-savvy, multi-skilled workers who can perform several tasks and troubleshoot with minimum supervision is huge. We’re basically looking at an entirely new type of worker.
Training and development in the manufacturing industry must shift its focus to skills in the technology sector. And that’s not enough. Personality traits like critical thinking, initiative, and independence are highly sought after, too.
The problem is, advanced and highly specialized skills like programming or automation can’t be taught from scratch. Still, anyone with some familiarity with computer technologies can learn how to operate automated equipment and work with computerized systems.
Using an LMS in manufacturing training will help you set up new courses quickly and with no hassle. Plus, what better way to enhance digital skills than by learning in an online environment?
LMSs allow you to create great content for soft skills training, too. Take critical thinking skills, for example. Using an LMS, you can create branching scenarios during which your employees will be called to make certain decisions and (safely) experience the outcomes. In time, they’ll feel confident enough to take initiative and respond to emergencies on their own.
2. Manufacturing Training Can Be Chaotic
Training in the manufacturing sector is not limited to workers and hard skills training. It extends to other departments, too, and takes several forms. Interrupting work to attend training could disrupt the daily flow. And that can lead to underperforming.
On top of that, manufacturing companies often operate across several sites, cities, and, in some cases, countries. Having to arrange and coordinate multiple training courses is insanely costly and time-consuming.
What’s even more troubling is that you can’t be sure whether every employee has received the same quality of training.
Online courses don’t require special premises or fixed training schedules. So, you can forget about one of the major manufacturing training challenges: time and location.
An LMS can also host an unlimited number of courses for all different types of skills and tasks. Even if you want to teach a practical skill like machine operation, you can take part in the training online. You can start the training with introductory videos and simulations to ease workers in. Then, move on to the practice session.
Perhaps, the greatest benefit of an LMS for manufacturing training is that it streamlines your training efforts. An LMS like TalentLMS not only offers the same learning material to all. It also sends notifications for course updates or certificates that have expired. This way, you can be sure that every employee is trained to the same standards and is aware of all the latest regulations and work procedures.
3. The Need To Keep New Talent Is Imperative
The skills shortage has led to many manufacturing jobs remaining open for quite a while. Which is all the more true for demanding (skill-wise) jobs, like skilled production or operations management.
The need to hold on to skillful employees that join the industry is growing. This makes onboarding one of the rising issues of training and development in manufacturing.
Training new manufacturing workers is unnegotiable. A positive onboarding experience helps them adapt faster and decreases turnover.
Enter the LMS. Any course that you create on an LMS is reusable and easy to update. To that end, using an LMS to deploy online or blended onboarding training has a double benefit. It minimizes unnecessary cost, and it saves you from the trouble of going through the onboarding process again and again.
What is more, an LMS offers learning delivery methods that help employees retain new information faster. Microlearning, in particular, is a jack up your sleeve when it comes to onboarding. It offers essential-only information, carefully organized in small chunks. Be it a short welcome video, an infographic outlining basic anti-harassment policies, or a mini-quiz to recap the key points, the choices are plenty.
4. Compliance Regulations Are Ever-Changing (Yet Essential!)
Compliance is undeniably among the top manufacturing training challenges today. Health and safety procedures, environmental laws, and general regulations are updated once too often. As a result, a considerable part of training in the manufacturing industry revolves around them.
There are two main issues regarding compliance training. First, it often involves complicated concepts or procedures. Which makes it not only hard to follow but also not well received.
What is more, the implications of non-compliance are serious and potentially dangerous. Which is why manufacturing trainers and managers must make a point of double-checking the effectiveness and status of compliance training.
A flexible LMS helps you stay on top of your compliance training. For starters, you can view at a glance which employees have completed their courses successfully and which haven’t.
The LMS automatically reassigns courses for certifications that have reached their expiration date. That’s one big responsibility off your hands.
What is more, it offers different types of learning content that make compliance training more engaging and maximize its effectiveness. eLearning simulations, for example, are an excellent way to demonstrate workplace safety procedures. The manufacturing workers practice under what feels like real-life circumstances. So, when an emergency occurs, they’re more likely to remember the steps they need to take and handle the situation effectively.
5. Manufacturing Training Is Costly
Trainer fees, travel, venue, accommodation expenditures: cost is one of the largest challenges faced in training and development for manufacturing employees. Add to that the extent manufacturing training can take for larger companies, and it’s safe to say that the cost skyrockets.
On-site training is also time-consuming, especially when it’s held on different premises. It takes hours or even days off your employees’ workday. This slows down production and weighs more responsibilities on the remaining workers. And you already know that lost productivity equals lost profit.
Moving part of your manufacturing training online with an affordable LMS like TalentLMS helps cut down costs. Plus, you can update and reuse your training course as many times as you need.
An LMS also offers trainees incredible flexibility on when and how they will access the course. For example, they can spend time on the job when the workload is heavy and do their training from home, or when they’re less busy. In any case, you can be sure that training will not take its toll on production time.
Conclusion
There are many training challenges in manufacturing. And the skills shortage adds to the pressure to overcome them fast. But with the help of an LMS, you can build a highly-skilled workforce that keeps up with the demands of the new manufacturing workplace.
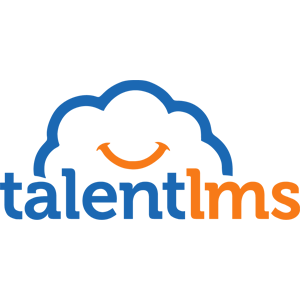