How To Improve Performance With A Personalized Blended Learning Approach
This article is part of a series exploring the concept of blended learning for remote and on-site workers. What you are about to read is a fable. The company, AshCom, is fictional but the learning challenges faced by Kathryn, AshCom’s CLO, and her team are real and commonly shared by learning teams in large organizations. It is our hope that you will be able to connect with the characters, their challenges, and the solutions they discover. We also invite you to read the first eBook in the series.
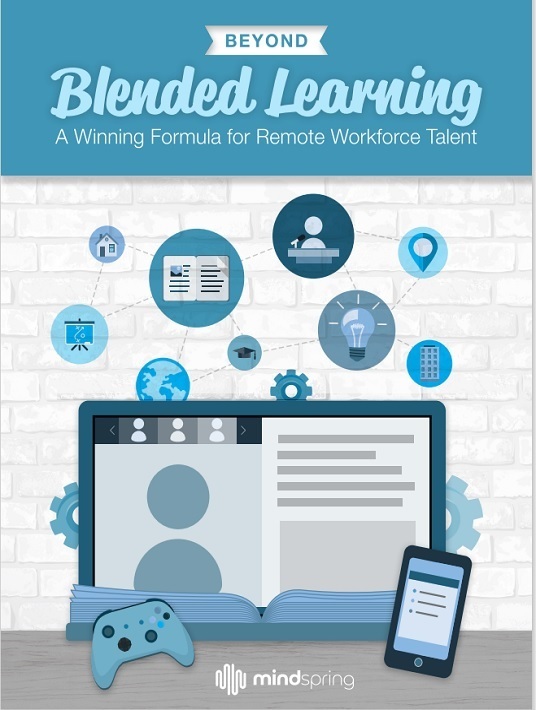
The Chief Operating Officer
A saltwater fish tank lined the wall of the corner office. Inside, the long antennae of a tiger pistol shrimp remained in constant contact with the yasha goby skimming the bottom. The weak-sighted shrimp dug burrows as the goby kept a close lookout against predators. The burrows made a quick getaway for both when danger appeared. “Some partnerships truly are a matter of survival,” thought Laszlo.
As the Chief Human Resource Officer at AshCom, it was in Laszlo’s professional interest to have a good relationship with Akihiko, the Chief Operating Officer. Laszlo got a direct line on the company’s people needs to achieve its operational and financial objectives. Akihiko knew he was reliant on Laszlo’s ability to attract, develop, and retain top talent to the 7,000-person company. There was a mutual benefit to them working well together.
What began as a good business relationship developed into mutual admiration and eventually into a friendship. The two often ate their lunch together. If their busy schedules allowed, they would occasionally have a drink after work. Every few months, they would have dinner with their spouses on the weekend.
Both had a global perspective. Laszlo had roots in Hungary and, before coming to AshCom, spent time in a global consulting company, Boeing, and Lincoln Financial. He read digital newspapers from around the world, partly for personal interest but also because he understood that the global manufacturing landscape would have an impact on AshCom.
Global Competition
Akihiko had grown up in Japan and attended a prestigious university earning an engineering degree with an emphasis in lean manufacturing. He spent 5 years working at one of Germany’s Big Three automotive manufacturing while earning certifications in lean manufacturing and Six Sigma. Minnesota might have seemed like an odd next step to a lot of his peers, but he met a member of the Ash family at a manufacturing conference in Brussels and the two discovered they shared a passion for lean manufacturing. They stayed in contact and when the Chief Operating Office position became available, Akihiko was AshCom’s first choice.
The conversations between Laszlo and Akihiko tended to return to the same general topics. They spoke often of how AshCom was now competing globally as was any other manufacturer of any size. Prices were being driven down in the face of increased international competition.
Both knew that they needed to find new ways to be more efficient while also learning to do more with less. Often, that meant heavy investment in technology and automation.
One night, having a beer after work, the two leaders dug deep into some of their challenges. “Automation solves one problem,” said Akihiko, “but it creates another. Our people need to have ever-increasing skill levels if the machines they control are going to run at peak efficiency. More tech means more skills. More knowledge.”
He continued, “I need more people with higher skills. But I also need a steady influx of people with basic skills who can quickly develop. I think some of our onboarding and ongoing training is moving more slowly than it should.”
Onboarding And Skill Development
Laszlo responded, “Tell me about that. Of course, I know we have onboarding and ongoing skill development programs. I can’t say I’ve looked carefully at them. Tell me what you are seeing.”
“Much of it comes down to three metrics,” said Akihiko. “These are things I watch constantly. Global competition means that everyone else watches these too. I have to find a way to increase our tool utilization time.”
“Just so I’m clear,” responded Laszlo, “you mean the total time a particular machine or tool can run, correct?”
“Exactly,” said Akihiko. “Every time we have to shut down a machine, we lose productivity. Sometimes a machine goes down because something isn’t being maintained properly. Other times, we have to shut down a machine or a line because we need to train people how to run it, maintain it, or fix it. When I see that happening, I know it is necessary, but I am watching dollars go down the drain.”
“Ok,” said Laszlo, “I get that. What else gives you heartburn?”
“At least two other things,” replied Akihiko.
“The first is I am constantly on a hunt to reduce expenses. Tool utilization means finding a way to make sure. Think about trying to do that while also decreasing our operating expenses. Any engineer could find a way to increase output by spending more money. We have to find a way to do that while spending less money.”
“And the last one?” said Laszlo.
“Defects,” said Akihiko. “We might be able to increase production. We might even find some ways to decrease our costs. But there is an inherent danger that a lot of people don’t consider. Let’s say that your production goes up 10% and you decrease your expenses by 10%. Everyone is happy, yes?”
“I would think so,” said Laszlo.
“They are right up until we realize we are making a lot more mistakes and our scrape rates have tripled. These are parts that either need to be thrown away or reworked, which are incredibly expensive to sort, store, and fix. It also causes major strain in our relationships with our clients.”
“And I imagine this isn’t always discovered right away?” asked Laszlo.
“Sometimes it is immediately noticed,” said Akihiko. “But sometimes it takes weeks or even months before we discover the problem or understand how bad it has become. It gets even worse when defects show up at our clients’ location.”
“Sounds like you are gently leading me to a place where I recognize that we have an HR problem. Or more directly, that I need to be part of the solution,” said Laszlo now laughing.
“You are a wise man,” said Akihiko. “You asked me to tell you my challenges, but I think these really are ‘our’ problems.
“There is something else,” continued Akihiko. “It is harder than just getting people to know what to do or giving them more skills. Lean manufacturing mostly happens between peoples’ ears. It is a mindset. It is learning to see things differently. It is always being on the lookout for a way we can improve. At some level, it is a belief system. It is a way of being, not just a way of doing.”
Is Blended Learning The Best Approach?
“And you think training is the solution?” asked Laszlo.
“Only one part, but a very significant part for certain,” said Akihiko. “But it might also just create one more problem for me. To train people, I have to pull them off their machines. I have to put them in a classroom. In some cases, I have to shut down a line, as I mentioned, because people need to be trained on it, or because I don’t have enough people on the line to safely operate it without creating a huge number of defects.” Akihiko burst out laughing when he noticed Laszlo jotting notes on a napkin. “I guess you didn’t come prepared for an in-depth discussion about lean manufacturing principles?”
“Look,” said Laszlo, “I love our 50,000-foot conversations about global trends. But I’ve known you long enough to know when you are feeling some stress. This is important to you, so it is important to me and AshCom.”
Akihiko was grateful for Laszlo’s friendship. Rather than take the attitude that this was someone else’s problem, Laszlo was willing to dive in and see if he could help.
“Oh, and more bad news for your napkin,” said Akihiko. “There is a supply issue.”
“Of machines and parts?” asked Laszlo.
“No,” replied Akihiko. “That’s not what I meant. There is a people supply problem. A lot of our people are retiring. It is only going to speed up in the next few years. Every time we hold a retirement party, I think of all the institutional knowledge that is walking out. I’m not sure how that is being captured or transferred to new people. Our technicians need to be highly technical people. Those who have been around a while have learned by decades of experience. How will we teach this to the declining number of young people who are interested in manufacturing?”
“I don’t need to take notes on that,” said Laszlo. “I hear that every week on our phone call with the HR teams in all the plants.” Akihiko paused for a moment and said,
“What they might not know is that the actual job of a technician is getting more challenging. We need people with strong math skills who can read a blueprint, accurately take measurements, maintain a machine, and inspect parts. We also need them to understand a process chart and some basic programming.”
Rise And Falls
Laszlo took a sip of his beer before he responded. “Skills and machine time need to go up. Cost and the time machines are offline needed to go down. Oh, and you are losing some of your most skilled people to retirement while fewer younger people are interested in working in manufacturing. And all the while, every one of our global competitors is trying to do the same thing, so that clock is ticking. Does that about cover it?”
“Yes,” said Akihiko. “Can you fix all of those things? Maybe by next week or the week after?”
“Sure. Consider it done,” said Laszlo with a slight eye roll. “You want to hear about my problems?”
“Not really,” replied Akihiko with a broad smile.
“Well, too bad,” said Laszlo. “I have to get home soon, but it seems like a lot of our current team members and those we are trying to recruit are asking about work-from-home options. Or flex time. Some want to know if they can work 100% remotely. Have you heard much of that?”
“In all seriousness,” said Akihiko, “I have a few times. Maybe more than a few times. How will that work in a manufacturing environment?”
“Great question,” said Laszlo. “The real answer is that I don’t know. You need more people being trained to higher skill levels. The people we need to train want more flexible work schedules and less time in the plant.”
“You are getting pulled in two directions,” said Akihiko. “I guess I hadn’t thought about how big the challenge will be to fix my problem when team members are going in the other direction. Who helps you figure this out?”
“I’m not sure,” said Laszlo, “but I know a good place to start. Kathryn is a solid Chief Learning Officer. She and her team have built some incredible learning experiences. It is probably a good time to present to her both of these challenges and see what she and her team figure out.”
The two colleagues shook hands. Driving home, Laszlo wondered how easily sleep would come to him that night. There was a lot on his mind, and the stakes seemed to be going up.
Conclusion
Download the eBook Beyond Blended Learning: A Winning Formula For Remote Workforce Talent to discover how AshCom overcomes its L&D challenges using innovative blended learning strategies. Also, join the webinar to uncover valuable insights that will help you improve your L&D planning and learning delivery.